Fabric mills play a crucial role in transforming raw fibers into the wonderful fabrics we use in Fashion and Home textile production. Have you ever wondered where these fabric mills obtain their raw materials? In this blog post, I’ll delve into the sourcing practices of fabric mills, focusing on Cotton and Polyester fibers and explore why fabric mills utilise raw fibers from multiple sources to produce fabric lengths.
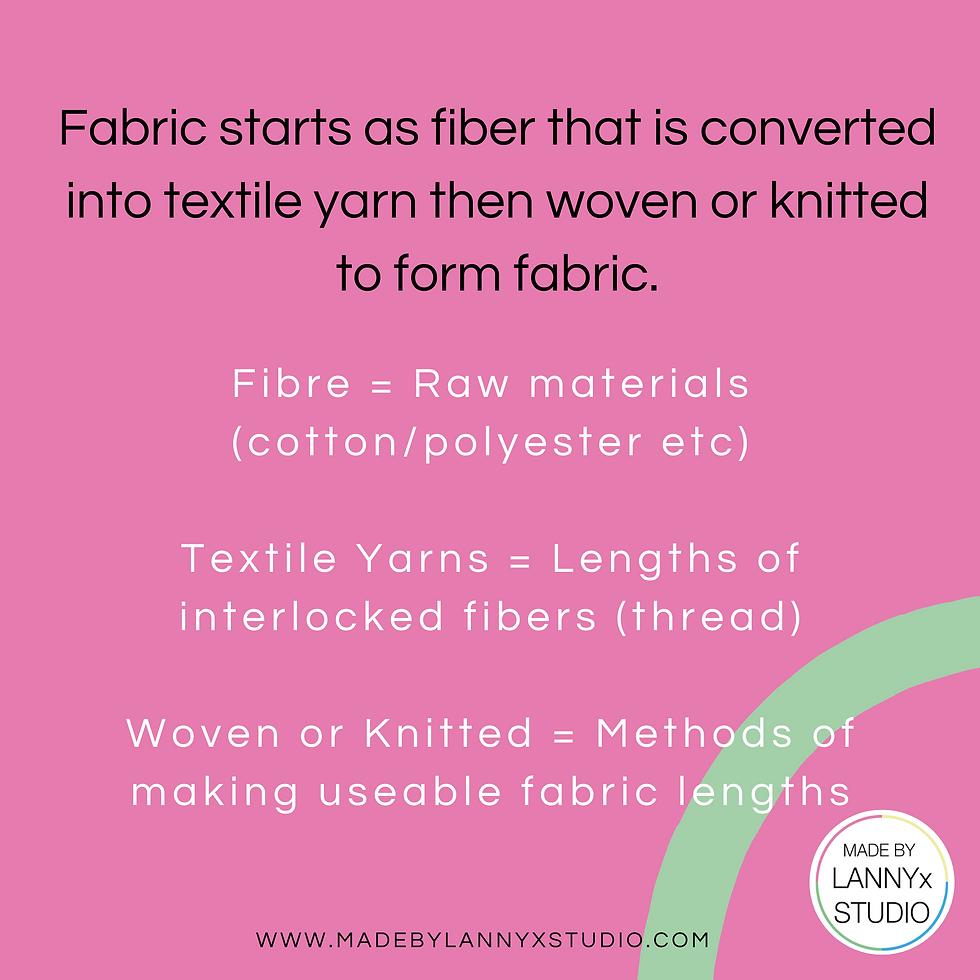
Sourcing Cotton Fibers:
Fabric mills acquire cotton fibers from various suppliers and regions around the world. Cotton farms act as primary sources, with countries like the United States, China, India, and Brazil being significant producers. Cotton farmers cultivate the crop and sell the harvested fibers to fabric mills directly or through intermediaries such as cotton merchants and brokers. Cotton cooperatives and commodity exchanges also serve as potential sources, offering quality control, logistics and financing solutions. Major players in the production of cotton fiber (not cotton growing) are Vardhman Group (India), Parkdale Mills (United States), Huafu Fashion Co., Ltd (China) and Olam International who operate in several countries such as the United States, Brazil, and various African nations.
Sourcing Polyester Fibers:
Polyester fibers, unlike cotton are synthetic fibers derived from petroleum-based products. Fabric mills procure polyester fibers from specialised manufacturers that produce synthetic fibers. These manufacturers employ advanced processes, such as polymerization, spinning, drawing and texturing to transform raw materials such as crude oil or natural gas into polyester fibers suitable for fabric production. Major players in the production of polyester fiber are Reliance Industries Limited (India), Sinopec Yizheng Chemical Fiber Company (China), Toray Industries (Japan), Alpek Polyester (Mexico) - To note most of these companies also have operating facilities outwith their base country in places like Thailand, America and Europe.
Image 1 - Ginned organic cotton fiber - Image courtesy of: ecologicaltextiles.com
Image 2 - Polyester staple fiber - Image courtesy of vnpolyfiber.com
Multiple Source Blending:
Fabric mills often blend raw fibers from multiple sources, not to be confused with blending different fibre types (i.e cotton with linen or cotton with polyester etc). Sources refers to the place fibres come and often fibers from different companies and regions are blended together to create fabric lengths and theres quite a few reasons why, this practice brings forth several advantages that contribute to the versatility and quality of the fabrics produced.
What Are The Advantages:
1- Enhancing Fabric Properties
Blending fibers from multiple sources allow fabric mills to combine different fibers unique characteristics, this results in fabrics with enhanced properties. For instance, combining long-staple cotton fibers for strength with short-staple cotton fibers for softness produces a fabric that strikes a balance between durability and comfort.
2- Consistency and Uniformity
By blending fibers from multiple sources, fabric mills can ensure consistent fabric quality. Carefully controlled blending ratios help minimise variations in fiber properties, resulting in fabrics with uniform characteristics throughout. This consistency is essential for meeting industry standards and fulfilling customer expectations.
3-Cost Optimisation
Blending fibers enables fabric mills to optimise cost while maintaining fabric quality. By utilising different fibers with varying price points, fabric mills can strike a balance between performance and affordability, making fabrics accessible to a wider market.
4-Customisation and Innovation
Blending fibers grants fabric mills the flexibility to create customised fabrics tailored to specific market demands. Through experimentation and innovation, fabric mills can develop unique fabric compositions with distinctive properties and aesthetics, setting themselves apart in the market.
A perfect example of fibre blending would be when you see the combination of Cotton and Organic Cotton, it’s often frustrating for people when they look at something that a mix of Cotton and Organic Cotton as it appears to be done specifically for cost reasons (and that may sometimes be true) but is not always the case, it can often be that the Organic Cotton fibers had to be blended with Standard cotton fibers from another source to create a specific weight, quality or even handfeel.

Image courtesy of Oeko-Tex.com
Disadvantages of Multplie Source Blending:
One of the disadvantages of multiple source blending is the difficulty to identify the specific supplier or region from which they acquire a fiber due to the complex supply chains involving multiple intermediaries highlighted above. There is also a lack of comprehensive traceability systems in the textile industry, limited documentation and labeling, although efforts are underway within the industry to improve this. These factors collectively pose challenges in pinpointing the exact origin of a fiber and is something I will delve into in another blog post.
Key Takeaway
Fabric mills often blend fibers from multiple sources to create fabric lengths, resulting in enhanced properties, consistent quality, cost optimisation, and customisation. While it is challenging for fabric mills to identify the specific supplier or region of a fiber, the practice of blending fibers offers versatility and quality in fabric production.
Next time you run your fingers across a piece of fabric, take a moment to appreciate the journey of the raw fibers that went into its creation, representing the ingenuity and skill of fabric mills worldwide.
Comentarios